Automatisierung und Optimierung im Stahlbau durch 3D-Multisensorik und Handhabungssysteme
Der fortschreitende Drang nach Digitalisierung und Innovation hat den Stahlbau vor neue Herausforderungen gestellt. Während die Branche ständig nach effizienteren Produktionsmethoden sucht, wird die Notwendigkeit einer automatisierten Qualitätssicherung immer offensichtlicher. Traditionelle Methoden stoßen an ihre Grenzen, wenn es um Präzision und Effizienz geht.
In einer Welt, in der Produktionstechnologie ständig weiterentwickelt wird, stand der Stahlbau vor dem Bedarf, sich anzupassen und zu innovieren. Es wurde deutlich, dass eine Revolution in der Branche notwendig war.
Das Forschungsteam des Projekts „3D-Multisensorik und Handhabungssysteme für die Automatisierung im Stahlbau“ hat diese Herausforderung erkannt und ergriffen. Sie verstanden, dass die Kombination von fortschrittlicher Sensortechnologie mit Roboterhandhabungssystemen der Schlüssel zur Lösung dieses Problems war.
Die Idee
Die Entwicklung eines Systems, das den gesamten Produktionsprozess im Stahlbau von der Materialauswahl bis zur Endkontrolle optimiert.
Die Lösung
Das Ergebnis war die Implementierung fortschrittlicher 3D-Sensorik und Handhabungssysteme, die nicht nur den Produktionsprozess revolutionierten, sondern auch neue Standards in puncto Qualität und Effizienz setzten.
Dadurch wird eine hohe Gestaltungskomplexität, Überhänge, Detailgrad und Robustheit möglich. Bauten sind auf Indoor-Bedingungen angepasst, etwa an Temperaturschwankungen, Feuchtigkeitsgehalte oder Stäube. Für den Anwendungsfall der dekorativen Einbauten sollen präzise Strukturen bestenfalls direkt am Aufstellungsort gedruckt werden. Dabei wird beachtet, dass möglichst geringe chemische Zusätze verwendet werden, um eine kostengünstige Entsorgbarkeit als Betonbruch zu gewährleisten.
Der Prozess
Während der Projektphase arbeiteten mehrere renommierte Institutionen und Unternehmen zusammen, um sicherzustellen, dass das entwickelte System den Anforderungen der Branche gerecht wird. Mit Expertenfeedback und praktischer Anwendung wurde das System perfektioniert.
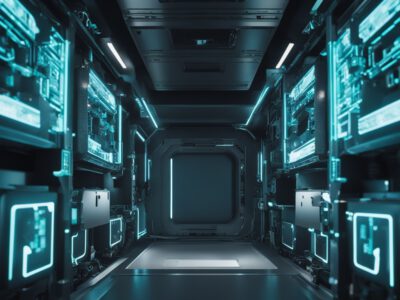
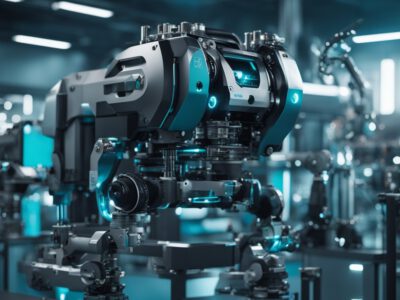
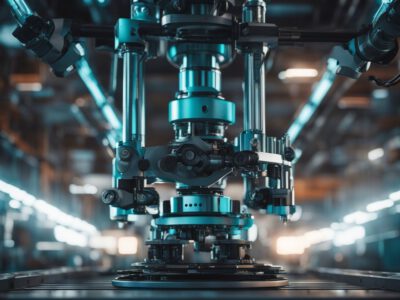
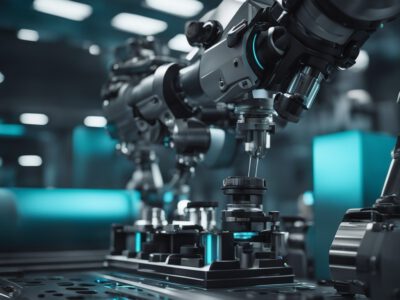
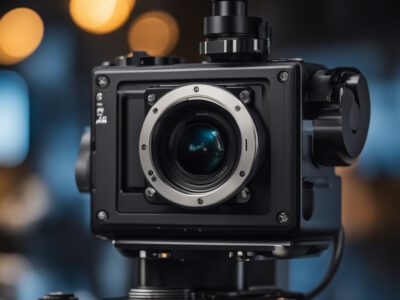
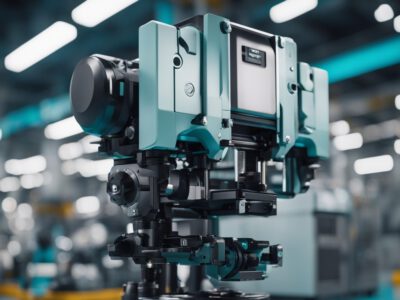
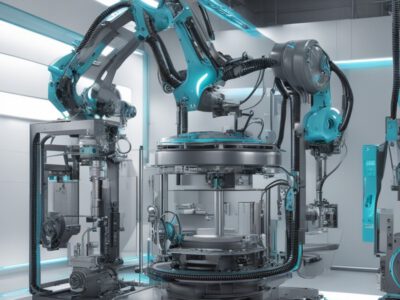
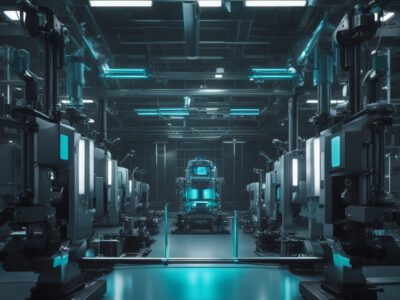
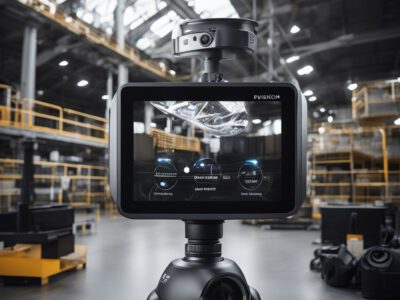
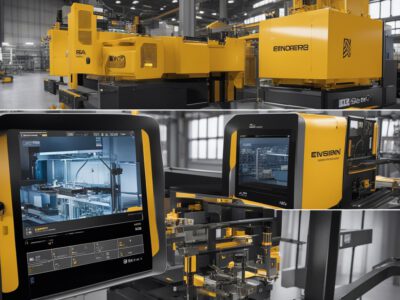
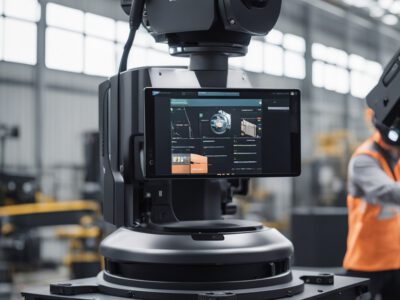
Das Ergebnis
Das Projekt hat mehrere Schlüsselkomponenten hervorgebracht. Eines der Hauptmerkmale ist die „Multimodale Datenerfassung und Analyse“, entwickelt von der Technischen Universität Ilmenau. Dieses System ermöglicht eine Echtzeit-Überwachung von Schweißprozessen, wodurch Fehler sofort erkannt und korrigiert werden können. Ein weiterer Durchbruch war das „adaptive automatisierte Kleinteileschweißsystem“ von Friedrich Motorsport. Dieses System passt sich an unterschiedliche Produktionsanforderungen an und bietet eine hohe Präzision beim Schweißen von Kleinteilen. Die Technische Hochschule Deggendorf hat zudem mit ihrem Projektteil eine Roboterlösung entwickelt, die in der Lage ist, schwere Lasten über große Arbeitsbereiche zu handhaben. Dies ist besonders im Stahlbau von großem Vorteil. Das Fraunhofer-Institut für Angewandte Optik und Feinmechanik IOF hat weiterhin den Weg für fortschrittliche Sensortechnologien im Stahlbau geebnet. Mit ihrer Entwicklung von „3D-Sensoriken für klein- und großräumige Prozesse“ wird die Geometrieerfassung, Bahnplanung und 3D-multispektrale Registrierung revolutioniert.
Mit der Einführung dieses Systems können Unternehmen im Stahlbau ihre Produktion optimieren, die Qualität ihrer Produkte sicherstellen und gleichzeitig die Produktionskosten senken.
Gefördert durch
Entwicklungszeitraum
2021 bis 2023
Gesamtinvestitionen
ca. 4.500.000 EUR
Fördersumme
ca. 2.400.000 EUR
Innovation
Fortschrittliche 3D-Sensorik und automatisierte Handhabungssysteme für den Stahlbau.
Motivation
Steigerung der Produktionseffizienz und Qualitätssicherung im Stahlbau.